Industrial & Commercial Process Chillers
Precision Cooling for Critical Processes
Process chillers remove heat generated during industrial and manufacturing processes by circulating a coolant, typically water or a water/glycol mix, through a closed-loop system. Unlike general-purpose HVAC systems, which prioritize occupant comfort, process chillers are engineered for the demands of production environments, where temperature stability is directly tied to quality and safety.
These systems support critical outcomes in sectors such as:
- Manufacturing and Industrial: Cooling equipment, stabilizing materials, and supporting continuous production
- Food and Beverage: Regulating temperatures for fermentation, cold storage, and thermal-sensitive processes that ensure product safety and flavour integrity.
- Pharmaceutical and Life Sciences: Ensuring precise environmental conditions for drug formulation, lab testing, and material storage in GMP-compliant facilities.
- Medical Imaging and Diagnostics: Providing consistent cooling for MRI machines, CT scanners, PET systems, and other heat-sensitive diagnostic technologies.
- Plastics and Rubber Manufacturing: Regulating mould temperatures and supporting extrusion processes for product consistency
- Breweries and Wineries: Supporting fermentation stability, clarification, cold crashing, and packaging conditions for product consistency and shelf life.
- Chemical Processing: Maintaining steady thermal conditions for heat-sensitive reactions and compound stabilization.
To explore broader solutions for high-stakes environments, visit our Mission Critical HVAC Systems page.
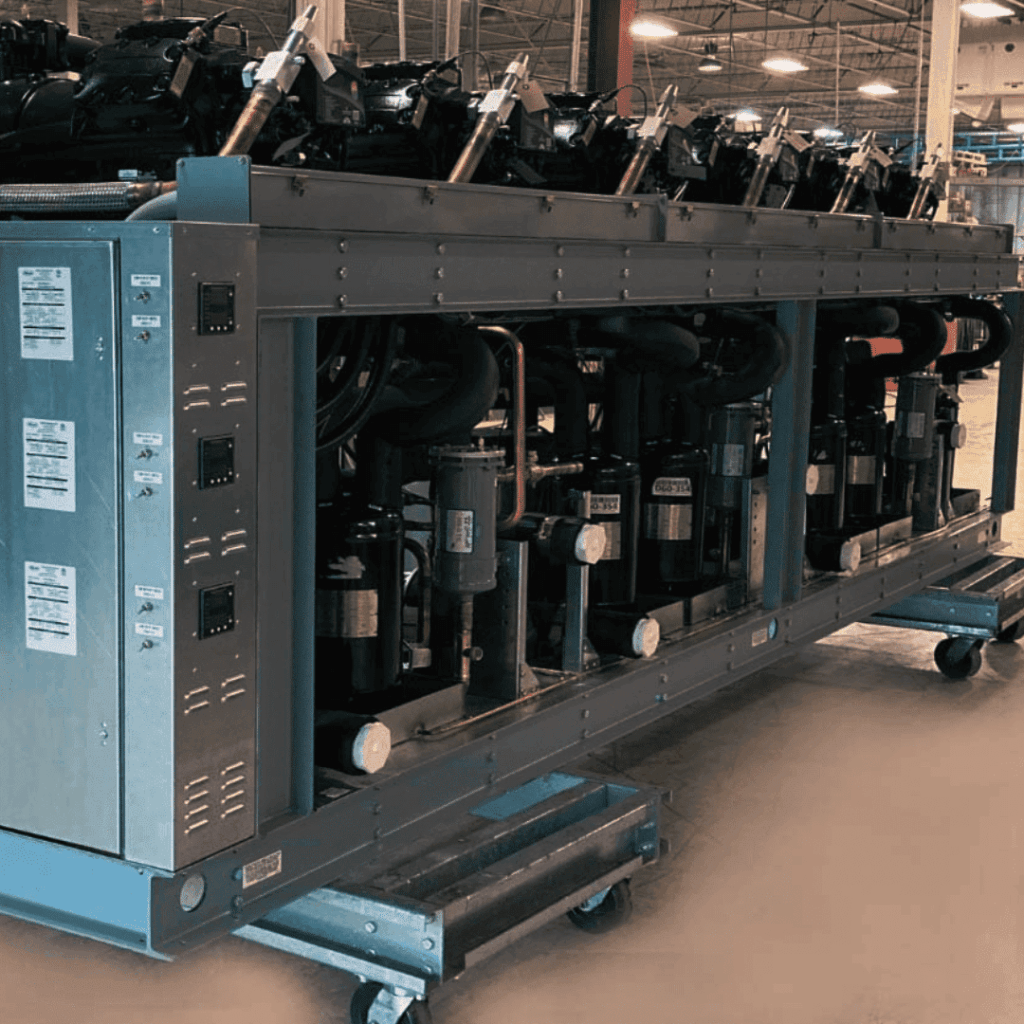
How Process Chillers Work
Every process chiller uses a closed-loop refrigeration cycle to absorb, transfer, and dissipate heat. The process is simple in theory, but optimized through advanced components and intelligent controls.
Core Components of Process Chillers:
- Compressor: Scroll, screw, or centrifugal compressors compress the refrigerant and enable heat transfer.
- Evaporator: Where process fluid gives up its heat to the refrigerant, essentially absorbing the process load.
- Condenser: Either air-cooled or water-cooled, the condenser releases absorbed heat into the surrounding environment.
- Pump System: Ensures consistent coolant flow and maintains system pressure.
Many process chillers also feature programmable control panels, alarms, and connectivity to building management systems for real-time monitoring and diagnostics.
Matching the System to the Application
Not all chillers are created equal. The right configuration depends on the environment, load profile, space availability, and cooling objectives. Lincoln Associates offers access to a full range of system types, helping clients find the best fit for their specific operational demands.
Types of Process Chillers:
- Air-Cooled Chillers: Ideal for outdoor installation and lower maintenance needs; popular for small to mid-sized operations.
- Water-Cooled Chillers: Highly efficient for larger facilities, though they require a water source and cooling tower.
- Portable Chillers: Compact, mobile units designed for temporary cooling needs or modular operations.
- Closed-Loop vs. Open-Loop Systems: Closed-loop designs minimize contamination risk and improve energy efficiency. Open-loop systems are simpler but more exposed to environmental variables.
Not sure what system is right for you? Use our Find a Rep tool for personalized guidance.
Key Considerations for Selecting a Chiller
The performance of a process chiller is tied directly to how well it aligns with its intended application. Our engineering team helps clients assess the following:
- Cooling Capacity: Correct sizing is essential to avoid short cycling or system strain.
- Energy Efficiency: Look for variable speed compressors, free cooling options, and energy recovery systems.
- Precision and Stability: Tighter temperature tolerances support higher quality outcomes and compliance in regulated environments.
- Environmental Impact: Low-GWP refrigerants and high-efficiency components support sustainability goals.
- Customization: We specialize in designing tailored systems that address legacy infrastructure, unique fluids, or physical constraints.
Explore our Manufacturing Partners for insight into the brands and technologies we represent.
Maintenance, Monitoring, and Support
Like any critical equipment, process chillers benefit from proactive maintenance and performance monitoring. Lincoln Associates provides full lifecycle support, ensuring long-term reliability.
Service & Support Includes:
- Routine Inspections: Assess refrigerant levels, compressor function, and control calibration.
- Preventative Maintenance: Regular coil cleanings, component testing, and electrical inspections extend system life.
- Troubleshooting & Repairs: Fast diagnosis and resolution of common faults like leaks, low-pressure conditions, or flow issues.
- Smart Monitoring: Integration with IoT sensors and building systems enables predictive maintenance and real-time alerts.
Learn more about how we support installed systems on our HVAC Services page.
Process Chillers from Lincoln Associates
Lincoln Associates delivers more than components; we deliver engineered solutions that advance your operational goals. Our process chillers are selected, configured, and supported with a deep understanding of the demands specific to your facility, whether that means maintaining uninterrupted production, achieving regulatory compliance, or optimizing energy consumption.
What Sets Us Apart:
- Tailored Engineering: We develop systems based on your actual process conditions and physical space—not generic templates.
- Top-Tier Components: All chillers are built with durable, efficient parts from manufacturers we trust.
- Fast Delivery & Support: Local reps, streamlined coordination, and responsive service keep your project moving.
- Sustainability Focus: We align system design with energy goals, green building standards, and refrigerant regulations.
For a full view of available systems and components, have a look at our Line Card.
Built for Long-Term Performance
Lincoln Associates delivers more than equipment, we provide systems designed for reliable operation, energy efficiency, and long-term value. From initial planning and equipment selection to installation support and ongoing service, we will ensure that your process chillers align with your performance goals, facility needs, and industry standards.
Every solution is backed by technical expertise, durable components, and a relentless focus on operational excellence.
Start Your Process Chiller Project
If your facility requires reliable and precise cooling, Lincoln Associates is ready to assist. Our team will work with you to evaluate system requirements, identify the right configuration, and coordinate implementation with unmatched attention to detail and responsiveness.